
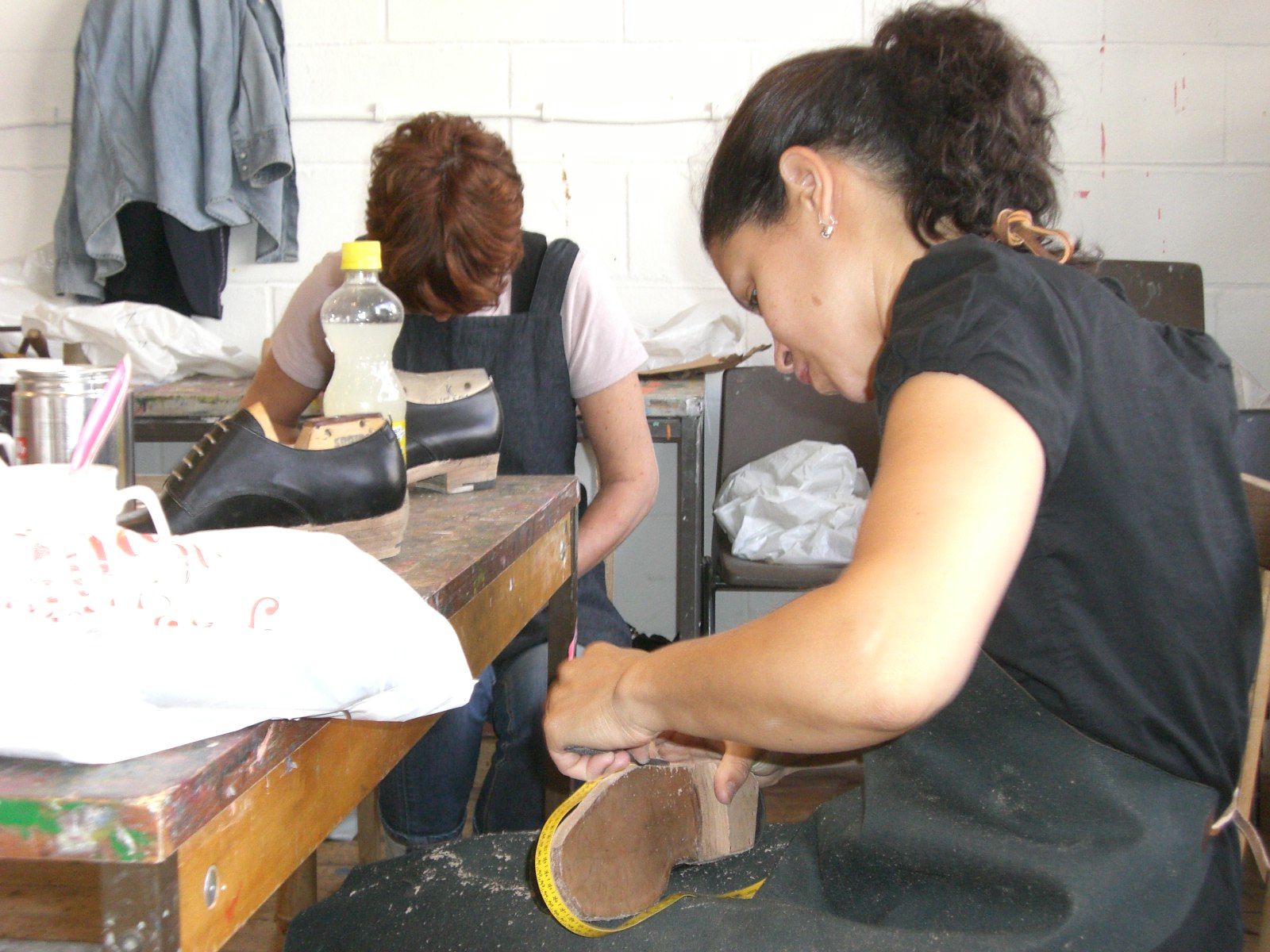
Testing out springy shoes full#
Grips and fixtures: Catalogs full of generalized and application-specific grips are offered by compression tester manufacturers and grip specialists. Using a 1,000 lbF sensor with 0.5 lbF resolution would result in lower accuracy as a percentage of the reading. For example, a compression spring requiring 36 lbF is best served by a 50 lbF force sensor with 0.02 lbF resolution. Ideally, a force sensor should be used at no less than 5-10% of its range. Choosing the correct capacity optimizes accuracy and measurement resolution. Dual-column test frames also offer the advantage of unlimited depth clearance, ideal for oddly shaped or oversized samples.įorce sensor: A force sensor, or load cell, measures tension and compression forces, and is available in many force capacities. Higher capacities are often configured as double-column systems and may be hydraulically driven. Single-column electromechanical test frames are normally offered in many increments, such as 100 lbF (500 N), 300 lbF (1.5 kN), 500 lbF (2.2 kN), 750 lbF (3.4 k), and 1,500 lbF (6.7 kN). Select a test frame capacity appropriate to the expected maximum force. With motorized frames, the speed may be preset to ensure that tests are performed consistently. Test frame: Test frames, whether motorized or manual, produce the force necessary for the test.

This information will aid in selecting the required components of a complete system: Then, determine the expected maximum force, maximum sample dimensions, and maximum sample deformation or extension. The first step in configuring a compression tester is identifying the test objective. Machine control and data collection software.Most systems are universal, capable of both tension and compression testing, and consist of a few main components:
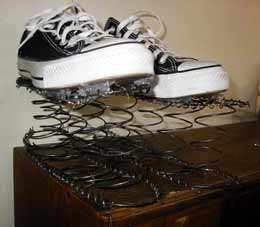
Compression testing may be done by benchtop force measurement systems.
